Cookie settings
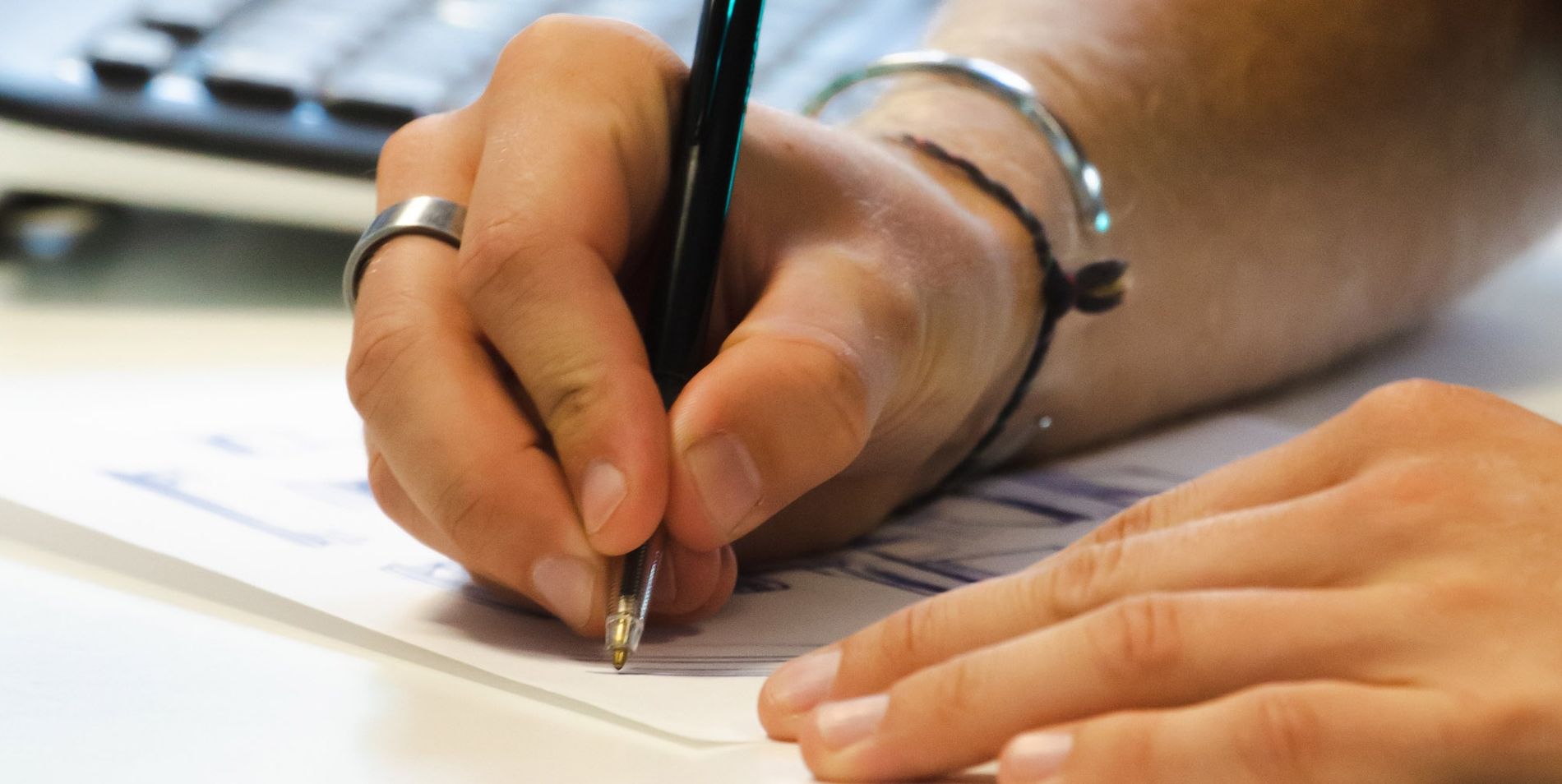
From Sketch to Invention: Inside Neonode’s Product Design Process
When Mechanical Engineer Eric Älfvåg isn’t painting cats in suits (yes, you read that right) he’s ideating new, creative solutions for Neonode's customers. Here, Eric shares a glimpse behind the scenes into Neonode’s internal design process.
Creative processes, especially in tech and product engineering, often consist of clearly defined steps and formal sprints. But sometimes, simply picking up a pen is the first, and best, place to start. The vision for Amazon was famously penned on a napkin, as well other pop-culture treasures like Harry Potter and Shark Week. And it’s no different at Neonode.
Our technology has been a linchpin for some of the world’s smartest products, including one of the first buttonless smartphones, an e-reader that can store over 3,000 books in the palm of your hand, and holographic coffee machines where you can order a cappuccino without touching a thing. But how does art and engineering intersect to make solutions like this possible? We spoke to Mechanical and Product Engineer (and artist) Eric Älfvåg to find out.
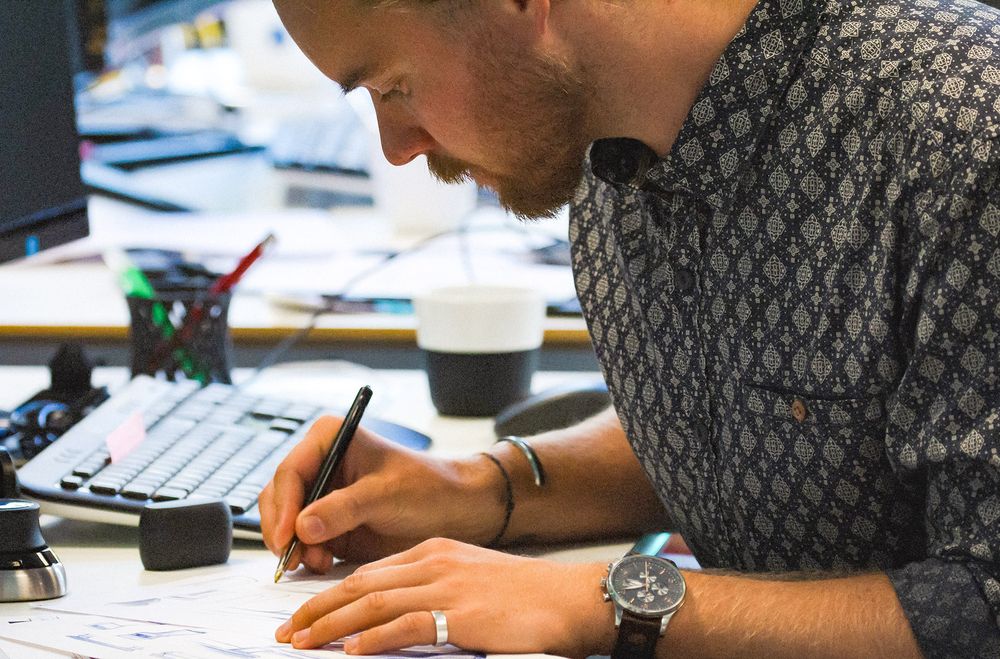
How would you describe Neonode’s internal design process?
Fluid! I’ll give you an example. One of the project managers came to me because he needed to create a holder for our Touch Sensor Modules (TSM). These are modules that can be retrofitted onto any screen or surface to give it a completely touchless interface using infrared light. A common application is self-service kiosks, for example at fast food restaurants and in airports. The issue is, they’re usually completely concealed in the customer’s hardware so people don’t notice it – but this isn’t very useful for product demos. We needed a way to mount the Touch Sensor Module (TSM) on the screen so it grabs attention and people can clearly see it and understand how it works.
The project manager had the idea of mounting the TSM at a distance from the screen in a branded bracket, and he drew a rough sketch to show me what he was thinking. I took that, and made some other quick sketches to generate more ideas. We kept going back and forth drawing on each others’ sketches and after a few rounds we narrowed the concept down. I took the one we chose and made some more detailed sketches with higher resolution and started thinking about the kind of materials and colors we could use. This was a solid foundation for the first prototype, and once the project manager was happy, I started 3D modelling it in CAD and created some renders to share with the manufacturing team.
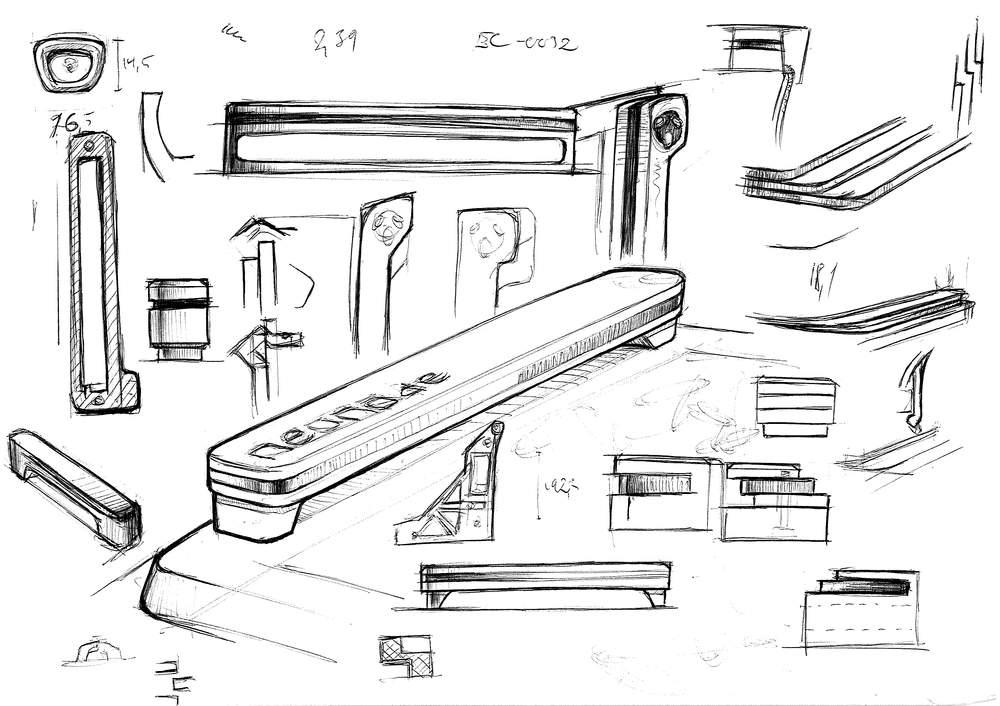
Initial sketches of Neonode's Touch Sensor Module Demo Holder
So what happens after the drawings?
Then it’s time for the engineering part. We had to make sure the design actually worked and that the TSM fitted inside it. We also needed to ensure the product could be mounted on the kiosk that it was designed for. So, I sent the CAD model with some technical drawings and requirements to be manufactured, and we collaborated to adjust it inline with what was needed to make the product a reality. I worked on everything from the initial sketches to installing and configuring the final product on the kiosk. The end result is exactly what we envisioned, so we were really happy.
How did you come up with the idea?
The project manager had two guiding concepts in his head from the start: sandwich and art deco. We needed something that was stacked on top of each other that could hold our TSM in place, and obviously art deco in style. The end result is a stylish bracket that has very clean lines and edges, and it’s definitely more ornamental than other holders out there.
It sounds like a fun project! Were there any challenges along the way?
The industrial design went really well but we hit a roadblock in the engineering phase. There needed to be a space for the TSM to send out infrared light and receive input signals, which was built into the middle layer. The output panel was supposed to be completely black so I planned to make this layer from transparent acrylic, which looks black, but is actually transparent to infrared light. But it didn’t really work with just a single layer of acrylic, so we redesigned it slightly to have a two-part middle layer. Solving challenges like this is common for us when we help our customers to create their own new designs and something we think is good fun.
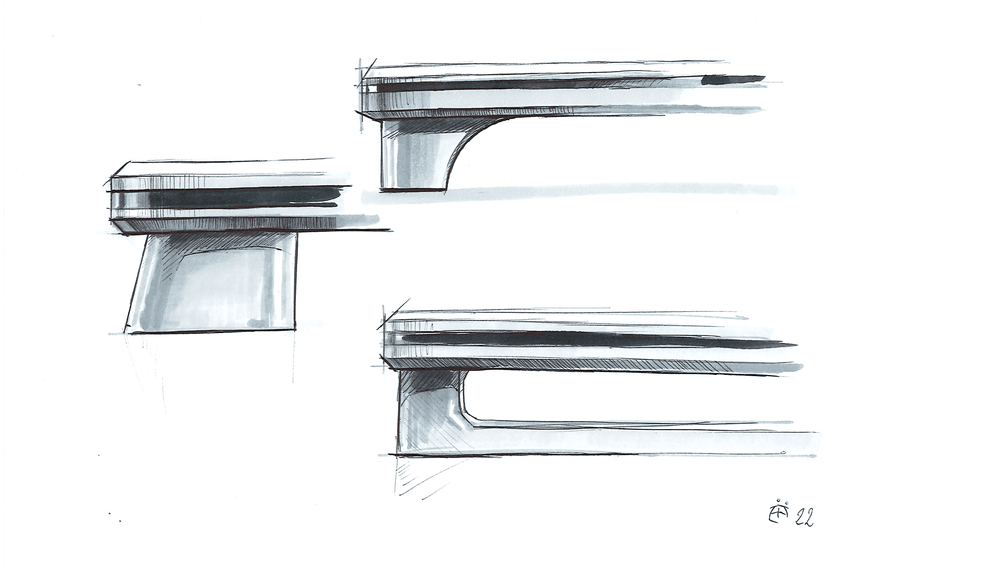
Touch Sensor Module 'sandwich' design.
What do you think is the most important thing in the product design process?
It doesn’t matter how good you are at drawing or how detailed it is, it’s just helpful to get something down on paper as it guides discussions more effectively than words. Sometimes you can say something and the other person agrees, so you think you have the same vision, but it looks totally different in your head. It’s easier to communicate the product vision with a drawing.
You also need to just talk to people and get as much feedback as possible. If I don’t get external advice and opinions, I’ll approach everything from my perspective, which isn’t always the right one. We try to work as one team in Neonode and it makes a big difference. The people here are really passionate too, which helps as they’re always happy to share their thoughts.
Can you tell us a little more about your background, and how you ended up at Neonode?
I’ve always been interested in expressing creativity through visual forms. I’ve been drawing and painting all my life, and after graduating high school I wasn’t really sure what I wanted to do so I ended up pursuing a degree in art history. But I decided I needed to do something less theoretical, and applied to study engineering at KTH. The program I chose was a mix between engineering and industrial design which suited me perfectly, as I like technology, and of course, design.
How do you find working at Neonode?
It’s really varied, and I get the chance to do a lot of different things and work on fun projects. I spend a lot of time designing prototypes in CAD and sending them off for manufacturing. We also have a 3D printer that we can use for quick and dirty proof of concepts, which is fun. I’ve been doing a lot of sketching and creating renders for the sales team to use as visual aids in customer conversations.
Do you still like to draw outside of work too?
I paint a lot of landscapes and also some portraits. I actually got commissioned to paint a friend’s cat in a traditional portrait style wearing a suit, which was super fun. I also do industrial design and product sketches in my spare time as well.
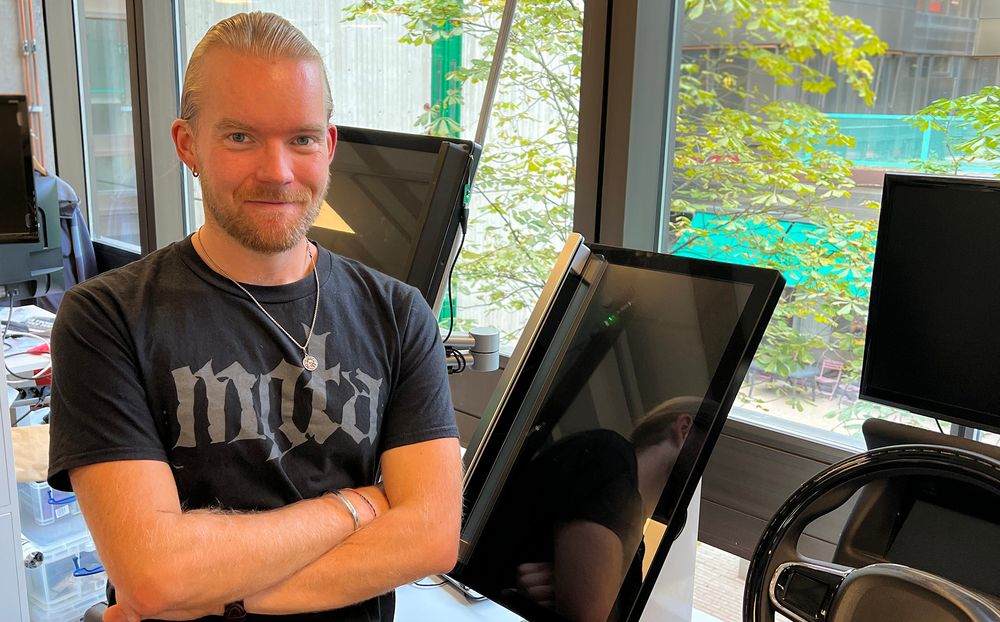